Founder of TriboNet, Editor, PhD (Tribology), Tribology Scientist at ASML, The Netherlands. Expertise in lubrication, friction, wear and contact mechanics with emphasis on modeling. Creator of Tribology Simulator.
Minimal Quantity Lubrication: Drop on Demand Printing Technique
Recent research (https://doi.org/10.1007/s40544-017-0183-5) has shown that about 23% of the world’s total energy consumption comes from the tribological contacts (moving parts subject to friction and wear, such as bearings, gears, etc.). This energy is lost, however, the use of the best tribological practices can reduce the energy consumption by up to 40% in the long term. Needless to say, that our society can greatly benefit from the developments in tribology and lubricataion research. In general, use of the best tribological and lubrication practices and research into new lubrication techniques can contribute towards several of the 17 United Nations sustainable development goals (United Nations, 2015), particularly, affordable and clean energy (reduced friction for efficient energy use), responsible consumption and production (reduced material waste), and climate action (reduced emission due to lower friction).
Today, most of the tribological contacts are lubricated. The lubricant’s main goals are reduction of friction and wear. It is very well known in the theory of Hydrodynamic Lubrication that in order to reduce friction in a tribological contact, it is necessary to separate the contacting solids (for example the rolling element and a raceway in a bearing) by a thin lubricant film. On the other hand, if the lubricant film becomes thick, the friction becomes high again. Clearly, the thickness of the lubricant film depends on the amount of a lubricant available for the lubrication. Therefore, there exist a minimum lubricant quantity that allows to avoid a contact between the moving surfaces and at the same time is not too thick to cause an increase of hydrodynamic friction. If this optimum amount is known and can be supplied to the contact, the best friction performance is achieved and the use of a lubricant is minimized. This is in line with the mentioned above United Nations sustainable development goals by reduction of friction and minimized used of a lubricant.
A recent research of the group led by Professor Cees Venner from University of Twente, The Netherlands made a good progress towards the industrialization of the minimum quantity lubrication approach. The group proposed a new method, so called drop-on-demand printing, as a method to achieve optimal (re)lubrication with a minimum lubricant quantity in a single ball contact.
The researchers applied the inkjet printing technology to develop their new method. In inkjet printing, liquid is ejected through a nozzle to form droplets that land on the surface. A piezo-acoustic or thermal actuator is used to generate a droplet. One of the main challenges in using this technology is that it is difficult to produce small droplets since the viscosity of lubricating oils is often much greater than the viscosity of inkjet fluids.
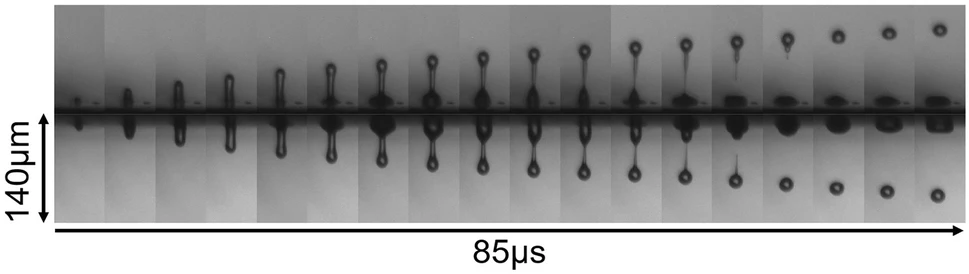
By means of a heated printing nozzle, it is possible to derive much smaller volume droplets for a higher viscous oil. It was demonstrated in the research that, with optical interferometry film thickness measurements, a build-up of a lubricant film from dry to fully flooded state can be realized using a drop-on-demand system that ejects oil droplets of only 3.3 pL. This is done in a controlled manner with an amount of lubricant of the order of nanoliters. From numerical simulations, it was shown that in the severely starved regime, 85% of the volume of each drop is actually ingested into the contact.
Besides the experimental technique, the researchers also developed a simple model to predict the behavior of the contact. The classical lubrication theories are well developed to predict the behavior of lubricated contacts for the cases when there is a lot of oil, so called fully flooded regime. However, these models are not suitable to predict the film thicknesses, when there is a shortage of oil, so called starved regime. In the minimum lubricant quantity lubrication, the contact operates in starved regime and the classical models cannot be applied. The developed model was validated using experimental results and showed a good agreement.
The research shows that lubrication by drop-on-demand printing is a promising technique, which can be used with full control in an experimental setup. Now it has to be extended to machine elements such as ball bearings and gears to improve control of friction and mitigate against wear by (re)lubricating contacts with minimal amount (droplets) of oil. This could lead to less energy losses due to friction, wear and lubricant waste.
Further information: van der Kruk, W.M., Smit, S.A., Segers, T.J. et al. Drop-on-Demand Printing as Novel Method of Oil Supply in Elastohydrodynamic Lubrication. Tribol Lett 67, 95 (2019). https://doi.org/10.1007/s11249-019-1208-1